Kemiske injektionslinjer nede i borehullet - hvorfor fejler de?Erfaringer, udfordringer og anvendelse af nye testmetoder
Copyright 2012, Society of Petroleum Engineers
Abstrakt
Statoil driver adskillige felter, hvor der anvendes en kontinuerlig indsprøjtning i borehullet af kalkinhibitor.Målet er at beskytte den øvre slange og sikkerhedsventilen mod (Ba/Sr) SO4 ellerCaCO;skala, i tilfælde hvor skalaklemning kan være vanskelig og omkostningsfuld at udføre på regelmæssig basis, f.eks. sammenkobling af undersøiske felter.
Kontinuerlig indsprøjtning af kalkinhibitor nede i borehullet er en teknisk passende løsning til at beskytte den øvre slange og sikkerhedsventil i brønde, der har afskalningspotentiale over produktionspakkeren;især i brønde, der ikke behøver at blive klemt regelmæssigt på grund af skaleringspotentiale i det nære brøndboringsområde.
Design, drift og vedligeholdelse af kemikalieinjektionslinjerne kræver ekstra fokus på materialevalg, kemikaliekvalificering og overvågning.Systemets tryk, temperatur, flow-regimer og geometri kan medføre udfordringer for sikker drift.Der er identificeret udfordringer i flere kilometer lange injektionslinjer fra produktionsanlægget til undersøisk skabelon og i injektionsventilerne nede i brøndene.
Erfaringer fra felten, der viser kompleksiteten af kontinuerlige injektionssystemer nede i borehullet med hensyn til nedbørs- og korrosionsproblemer, diskuteres.Laboratorieundersøgelser og anvendelse af nye metoder til kemisk kvalificering a repræsenteret.Behovene for tværfaglige tiltag behandles.
Introduktion
Statoil driver adskillige felter, hvor der er anvendt kontinuerlig injektion af kemikalier nede i borehullet.Dette involverer hovedsageligt injektion af kedelstensinhibitor(SI), hvor formålet er at beskytte den øvre slange og sikkerhedsventilen nede i borehullet (DHSV) mod (Ba/Sr) SO4ellerCaCO;vægt.I nogle tilfælde injiceres emulsionsbryder nede i hullet for at starte separationsprocessen så dybt i brønden som muligt ved en relativ høj temperatur.
Kontinuerlig injektion af kedelstensinhibitor nede i borehullet er en teknisk passende løsning til at beskytte den øvre del af brøndene, der har skaleringspotentiale over produktionspakkeren.Kontinuerlig injektion kan anbefales, især i brønde, der ikke behøver at blive klemt på grund af lavt afskalningspotentiale i den nære brøndboring;eller i tilfælde, hvor skalaklemning kan være vanskelig og bekostelig at udføre på regelmæssig basis, f.eks. sammenkobling af undersøiske felter.
Statoil har udvidet erfaring med kontinuerlig kemikalieinjektion til topside-systemer og undersøiske skabeloner, men den nye udfordring er at tage injektionspunktet længere dybt ned i brønden.Design, drift og vedligeholdelse af kemikalieinjektionslinjerne kræver ekstra fokus på flere emner;såsom materialevalg, kemisk kvalificering og overvågning.Systemets tryk, temperatur, flow-regimer og geometri kan medføre udfordringer for sikker drift.Udfordringer i lange (adskillige kilometer) injektionslinjer fra produktionsanlægget til undersøisk skabelon og ind i injektionsventilerne nede i brøndene er blevet identificeret;Fig.1.Nogle af indsprøjtningssystemerne har fungeret efter planen, mens andre er fejlet af forskellige årsager.Adskillige nye feltudviklinger er planlagt til kemisk injektion i borehullet (DHCI);imidlertid;i nogle tilfælde er udstyret endnu ikke fuldt kvalificeret.
Anvendelse af DHCI er en kompleks opgave.Det involverer færdiggørelse og brønddesign, brøndkemi, topside-system og det kemiske doseringssystem af topside-processen.Kemikaliet vil blive pumpet fra oversiden via kemikalieinjektionsledningen til færdiggørelsesudstyret og ned i brønden.Derfor er samarbejde mellem flere discipliner afgørende i planlægningen og udførelsen af denne type projekter.Forskellige overvejelser skal vurderes, og god kommunikation under designet er vigtig.Procesingeniører, undersøiske ingeniører og færdiggørelsesingeniører er involveret, der beskæftiger sig med emnerne brøndkemi, materialevalg, flowsikring og produktionskemistyring.Udfordringerne kan være kemisk pistolkonge eller temperaturstabilitet, korrosion og i nogle tilfælde en vakuumeffekt på grund af lokale tryk- og floweffekter i kemikalieinjektionsledningen.Ud over disse forhold som højt tryk, høj temperatur, høj gashastighed, højt skaleringspotentiale,langdistance navlestreng og dybt injektionspunkt i brønden, giver forskellige tekniske udfordringer og krav til det injicerede kemikalie og til injektionsventilen.
En oversigt over de DHCI-systemer, der er installeret i Statoil-driften, viser, at erfaringerne ikke altid har været succesfulde.Udfordringerne varierer fra felt til felt, og problemet er ikke nødvendigvis, at selve kemikalieindsprøjtningsventilen ikke virker.
I løbet af de sidste år er der blevet oplevet adskillige udfordringer vedrørende kemiinjektionslinjer nede i borehullet.I denne artikel gives nogle eksempler fra disse erfaringer.Papiret diskuterer udfordringer og foranstaltninger, der er truffet for at løse problemerne relateret til DHCI-linjer.Der gives to case-historier;en om korrosion og en om kemisk pistolkonge.Erfaringer fra felten, der viser kompleksiteten af kontinuerlige injektionssystemer nede i borehullet med hensyn til nedbørs- og korrosionsproblemer, diskuteres.
Laboratorieundersøgelser og anvendelse af nye metoder til kemisk kvalificering overvejes også;hvordan man pumper kemikaliet, skaleringspotentiale og forebyggelse, kompleks udstyrsanvendelse og hvordan kemikaliet vil påvirke topsidesystemet, når kemikaliet produceres tilbage.Acceptkriterier for kemikalieanvendelse involverer miljøproblemer, effektivitet, lagerkapacitet ovenpå, pumpehastighed, om eksisterende pumpe kan bruges osv. Tekniske anbefalinger skal baseres på væske- og kemikompatibilitet, restpåvisning, materialekompatibilitet, undersøisk umbilical design, kemikaliedoseringssystem og materialer i disse linjers omgivelser.Kemikaliet skal muligvis hydrathæmmes for at forhindre tilstopning af injektionsledningen fra gasinvasion, og kemikaliet må ikke fryse under transport og opbevaring.I de eksisterende interne retningslinjer er der en tjekliste over hvilke kemikalier der kan påføres på hvert punkt i systemet. Fysiske egenskaber såsom viskositet er vigtige.Injektionssystemet kan indebære 3-50 km afstand af umbilical undersøisk flowledning og 1-3 km ned i brønden.Derfor er temperaturstabiliteten også vigtig.Evaluering af nedstrømseffekter, f.eks. i raffinaderier, skal muligvis også overvejes.
Kemiske injektionssystemer nede i hullet
Omkostningsfordel
Kontinuerlig injektion af kedelstensinhibitor nede i borehullet for at beskytte DHS Vor produktionsslangen kan være omkostningseffektiv sammenlignet med at klemme brønden med kedelstensinhibitor.Denne applikation reducerer potentialet for dannelsesskader sammenlignet med kalkpressebehandlinger, reducerer potentialet for procesproblemer efter en skalaklemning og giver mulighed for at kontrollere kemikalieinjektionshastigheden fra topside-injektionssystemet.Injektionssystemet kan også bruges til at injicere andre kemikalier kontinuerligt nede i hullet og kan derved reducere andre udfordringer, der måtte opstå længere nedstrøms procesanlægget.
En omfattende undersøgelse er blevet udført med udvikling af en nedehullsskalastrategi for Oseberg S eller feltet.Den største skala bekymring var CaCO;afskalning i den øvre slange og mulig DHSV-fejl.Oseberg S eller skalastyringsstrategien konkluderede, at DHCI over en periode på tre år var den mest omkostningseffektive løsning i de brønde, hvor kemikalieinjektionslinjerne fungerede.Det vigtigste omkostningselement med hensyn til den konkurrerende teknik med scale squeeze var den udskudte olie snarere end de kemiske/driftsomkostninger.For anvendelse af kedelstensinhibitor i gasløft var den vigtigste faktor på kemikalieomkostningerne den høje gasløfthastighed, der førte til høj SI-koncentration, da koncentrationen skulle afbalanceres med gasløftningshastigheden for at undgå kemisk pistolkonge.For de to brønde på Oseberg S eller som havde velfungerende DHC I-linjer, blev denne mulighed valgt for at beskytte DHS V'erne mod CaCO;skalering.
Kontinuerligt indsprøjtningssystem og ventiler
Eksisterende kompletteringsløsninger, der anvender kontinuerlige kemiske injektionssystemer, står over for udfordringer for at forhindre tilstopning af kapillærledningerne.Typisk består injektionssystemet af en kapillarledning, 1/4” eller 3/8” udvendig diameter (OD), tilsluttet til en overflademanifold, ført igennem og forbundet til slangeophænget på den ringformede side af slangen.Kapillærledningen er fastgjort til produktionsslangens ydre diameter ved hjælp af specielle slangekraveklemmer og løber på ydersiden af slangen helt ned til kemikalieindsprøjtningsdornen.Dornen placeres traditionelt opstrøms for DHS V eller dybere i brønden med den hensigt at give det indsprøjtede kemikalie tilstrækkelig dispersionstid og at placere kemikaliet, hvor udfordringerne findes.
Ved kemikalieindsprøjtningsventilen, fig. 2, indeholder en lille patron ca. 1,5" i diameter kontraventilerne, som forhindrer brøndboringsvæsker i at trænge ind i kapillarledningen.Det er simpelthen en lille poppet, der kører på en fjeder.Fjederkraften indstiller og forudsiger det tryk, der kræves for at åbne ventilen fra tætningssædet.Når kemikaliet begynder at strømme, løftes tallerkenventilen fra sit sæde og åbner kontraventilen.
Det er påkrævet at have to kontraventiler installeret.En ventil er den primære barriere, der forhindrer brøndboringsvæsken i at trænge ind i kapillarledningen.Dette har et relativt lavt åbningstryk (2-15 bar). Hvis det hydrostatiske tryk inde i kapillarledningen er mindre end brøndboringstrykket, vil brøndboringsvæsken forsøge at trænge ind i kapillarledningen.Den anden kontraventil har atypisk åbningstryk på 130-250 bar og er kendt som U-rørsforebyggelsessystemet.Denne ventil forhindrer kemikaliet inde i kapillarledningen i at strømme frit ind i brøndboringen, hvis det hydrostatiske tryk inde i kapillarledningen er større end brøndboringstrykket ved kemikalieinjektionspunktet inde i produktionsrøret.
Ud over de to kontraventiler, er der normalt et in-line filter, formålet med dette er at sikre, at ingen snavs af nogen art kan bringe kontraventilsystemernes tætningsevne i fare.
Størrelsen af de beskrevne kontraventiler er ret små, og renheden af den indsprøjtede væske er afgørende for deres operationelle funktionalitet.Det menes, at affald i systemet kan skylles væk ved at øge flowhastigheden inde i kapillarledningen, så kontraventilerne åbner med vilje.
Når kontraventilen åbner, falder det strømmende tryk hurtigt og forplanter sig op gennem kapillærledningen, indtil trykket igen stiger.Kontraventilen vil derefter lukke, indtil strømmen af kemikalier opbygger tilstrækkeligt tryk til at åbne ventilen;resultatet er tryksvingninger i kontraventilsystemet.Jo højere åbningstryk kontraventilsystemet har, jo mindre flowareal etableres, når kontraventilen åbner, og systemet forsøger at opnå ligevægtsforhold.
De kemiske injektionsventiler har et relativt lavt åbningstryk;og hvis slangetrykket ved kemikalieindgangspunktet bliver mindre end summen af det hydrostatiske tryk af kemikalier inde i kapillarledningen plus kontraventilens åbningstryk, vil der opstå næsten vakuum eller vakuum i den øvre del af kapillarledningen.Når injektionen af kemikalier stopper, eller strømmen af kemikalier er lav, vil der begynde at forekomme nærvakuumforhold i den øverste sektion af kapillærledningen.
Vakuumniveauet afhænger af brøndboringstrykket, vægtfylden af den injicerede kemikalieblanding, der anvendes inde i kapillarledningen, kontraventilens åbningstryk ved injektionspunktet og kemikaliegennemstrømningen inde i kapillarledningen.Brøndforholdene vil variere over markens levetid, og potentialet for vakuum vil derfor også variere over tid.Det er vigtigt at være opmærksom på denne situation for at tage de rigtige hensyn og forholdsregler, før forventede udfordringer opstår.
Sammen med lave injektionshastigheder fordamper de opløsningsmidler, der bruges i disse typer applikationer, typisk og forårsager virkninger, der ikke er blevet fuldt ud undersøgt.Disse effekter er gun king eller udfældning af faste stoffer, for eksempel polymerer, når opløsningsmidlet fordamper.
Yderligere kan galvaniske celler dannes i overgangsfasen mellem væskeoverfladen af kemikaliet og den dampfyldte næsten-vakuum gasfase ovenfor.Dette kan føre til lokal grubetæring inde i kapillarlinjen som følge af kemikaliets øgede aggressivitet under disse forhold.Flager eller saltkrystaller dannet som en film inde i kapillarledningen, når dens indre tørrer ud, kan sætte sig fast eller tilstoppe kapillarledningen.
Brøndbarrierefilosofi
Ved design af robuste brøndløsninger kræver Statoil, at brøndsikkerheden er på plads hele tiden i brøndens livscyklus.Statoil kræver således, at der er to uafhængige brøndbarrierer intakte.Fig. 3 viser skematisk atypisk brøndbarriere, hvor den blå farve repræsenterer den primære brøndbarriereindhylning;i dette tilfælde produktionsrøret.Den røde farve repræsenterer den sekundære barrierekonvolut;huset.På venstre side af skitsen er kemikalieindsprøjtningen angivet som en sort linje med injektionspunkt til produktionsslangen i området markeret med rødt (sekundær barriere).Ved at indføre kemiske injektionssystemer i brønden bringes både de primære og sekundære brøndboringsbarrierer i fare.
Sagshistorie om korrosion
Rækkefølgen af begivenhederne
Kemisk indsprøjtning nede i borehullet af kedelstensinhibitor er blevet påført et oliefelt drevet af Statoil på den norske kontinentalsokkel.I dette tilfælde var den påførte kedelstensinhibitor oprindeligt kvalificeret til topside- og undersøisk påføring.Genkomplettering af brønden blev efterfulgt af installation af DHCIpointat2446mMD, Fig.3.Indsprøjtningen i borehullet af kedelstensinhibitoren på oversiden blev startet uden yderligere test af kemikaliet.
Efter et års drift blev der observeret lækager i kemikalieinjektionssystemet, og undersøgelser startede.Lækagen havde en skadelig effekt på brøndbarriererne.Lignende hændelser fandt sted for flere brønde, og nogle af dem måtte lukkes inde, mens efterforskningen var i gang.
Produktionsrøret blev trukket og studeret i detaljer.Korrosionsangrebet var begrænset til den ene side af røret, og nogle rørsamlinger var så korroderede, at der faktisk var huller igennem dem.Cirka 8,5 mm tykt 3 % kromstål var gået i opløsning på mindre end 8 måneder.Hovedkorrosionen var opstået i den øverste sektion af brønden, fra brøndhovedet og ned til ca. 380 m MD, og de værste korroderede rørsamlinger blev fundet ved ca. 350 m MD.Under denne dybde blev der kun observeret lidt eller ingen korrosion, men der blev fundet meget affald på rørets OD'er.
9-5/8'' kappen blev også skåret og trukket, og lignende effekter blev observeret;med korrosion i den øverste del af brønden kun på den ene side.Den inducerede lækage var forårsaget af sprængning af den svækkede sektion af kappen.
Materialet til den kemiske injektionslinje var Alloy 825.
Kemisk kvalifikation
Kemiske egenskaber og korrosionstest er vigtige fokuspunkter i kvalificeringen af kalkinhibitorer, og den faktiske kalkinhibitor havde været kvalificeret og brugt i topside- og undersøiske applikationer i flere år.Årsagen til at anvende det faktiske kemikalie nede i borehullet var forbedrede miljøegenskaber ved at erstatte det eksisterende kemikalie nede i borehullet. Kalkstensinhibitoren var dog kun blevet brugt ved omgivende topside- og havbundstemperaturer (4-20 ℃).Når det blev injiceret i brønden, kunne temperaturen af kemikaliet være så høj som 90 ℃, men der var ikke udført yderligere test ved denne temperatur.
Indledende korrosivitetstest var blevet udført af kemikalieleverandøren, og resultaterne viste 2-4 mm/år for kulstofstål ved høj temperatur.I denne fase havde der været minimal inddragelse af operatørens materialetekniske kompetence.Nye test blev senere udført af operatøren, der viste, at kalkinhibitoren var stærkt ætsende for materialerne i produktionsrøret og produktionskappen, med korrosionshastigheder på over 70 mm/år.Det kemiske injektionslinjemateriale Alloy 825 var ikke blevet testet mod kedelstensinhibitoren før injektion.Brøndtemperaturen kan nå 90 ℃, og tilstrækkelige tests skulle have været udført under disse forhold.
Undersøgelsen afslørede også, at kedelstensinhibitoren som koncentreret opløsning havde rapporteret pH <3,0.pH var dog ikke blevet målt.Senere viste den målte pH en meget lav værdi på pH 0-1.Dette illustrerer behovet for målinger og materialeovervejelser ud over givne pH-værdier.
Fortolkning af resultaterne
Indsprøjtningsledningen (fig. 3) er konstrueret til at give et hydrostatisk tryk af kalkinhibitoren, der overstiger trykket i brønden ved injektionspunktet.Inhibitoren injiceres ved et højere tryk, end der findes i brøndboringen.Dette resulterer i en U-rørseffekt ved lukning af brønden.Ventilen vil altid åbne med et højere tryk i injektionsledningen end i brønden.Vakuum eller fordampning i injektionsledningen kan derfor forekomme.Korrosionshastigheden og risikoen for grubetæring er størst i gas/væske overgangszonen på grund af fordampning af opløsningsmidlet.Laboratorieforsøg udført på kuponer bekræftede denne teori.I brøndene, hvor der blev oplevet lækage, var alle huller i injektionsledningerne placeret i den øverste del af kemikalieinjektionsledningen.
Fig. 4 viser fotografering af DHC I-linjen med betydelig grubetæring.Korrosionen set på det ydre produktionsrør indikerede en lokal eksponering af kedelstensinhibitor fra hullets lækagepunkt.Lækagen var forårsaget af grubetæring af stærkt ætsende kemikalie og lækage gennem kemikalieinjektionslinjen ind i produktionshuset.Aflejringsinhibitoren blev sprøjtet fra den fordybnede kapillarledning på kappen og rørene, og der opstod utætheder.Eventuelle sekundære konsekvenser af utætheder i injektionsledningen var ikke taget i betragtning.Det blev konkluderet, at foringsrør- og rørkorrosionen var et resultat af koncentrerede kedelstensinhibitorer, der blev bedt fra den fordybnede kapillarlinje videre til foringsrøret og røret, Fig.5.
I dette tilfælde havde der været manglende inddragelse af materialekompetenceingeniører.Ætsningsevnen af kemikaliet på DHCI-linjen var ikke blevet testet, og de sekundære effekter på grund af lækage var ikke blevet evalueret;såsom om de omkringliggende materialer kunne tåle kemisk eksponering.
Sagshistorie om den kemiske pistolkonge
Rækkefølgen af begivenhederne
Skalaforebyggelsesstrategien for et HP HT-felt var kontinuerlig injektion af kedelstensinhibitor opstrøms sikkerhedsventilen nede i borehullet.Et alvorligt calciumcarbonat-skaleringspotentiale blev identificeret i brønden.En af udfordringerne var høj temperatur og høj gas- og kondensatproduktionshastighed kombineret med lav vandproduktionshastighed.Bekymringen ved at injicere kedelstensinhibitor var, at opløsningsmidlet ville blive fjernet af den høje gasproduktionshastighed, og pistolkongen af kemikaliet ville forekomme ved injektionspunktet opstrøms for sikkerhedsventilen i brønden, Fig.1.
Under kvalificeringen af kedelstensinhibitoren var fokus på produktets effektivitet ved HP HT-forhold, herunder adfærd i topside-processystemet (lav temperatur).Udfældning af selve kedelstensinhibitoren i produktionsrøret på grund af den høje gashastighed var den største bekymring.Laboratorieforsøg viste, at kedelstensinhibitor kunne udfælde og klæbe til slangevæggen.Betjening af sikkerhedsventilen kan derfor overskride risikoen.
Erfaring viste, at kemikalieledningen efter et par ugers drift var utæt.Det var muligt at overvåge brøndboringstrykket ved overflademåleren installeret i kapillarledningen.Linjen blev isoleret for at opnå brøndintegritet.
Den kemiske injektionsledning blev trukket ud af brønden, åbnet og inspiceret for at diagnosticere problemet og finde mulige årsager til fejl.Som det kan ses i fig. 6, blev der fundet en betydelig mængde bundfald, og kemisk analyse viste, at noget af dette var kedelstensinhibitoren.Bundfaldet var lokaliseret ved tætningen, og tallerkenen og ventilen kunne ikke betjenes.
Ventilfejlen var forårsaget af snavs inde i ventilsystemet, der forhindrede kontraventilerne i at æde på metal til metalsædet.Affaldet blev undersøgt, og hovedpartiklerne viste sig at være metalspåner, sandsynligvis produceret under installationsprocessen af kapillarlinjen.Derudover blev der identificeret noget hvidt affald på begge kontraventiler, især på bagsiden af ventilerne.Dette er lavtrykssiden, dvs. siden vil altid være i kontakt med brøndboringsfluiderne.Oprindeligt mentes dette at være affald fra produktionsbrøndboringen, da ventilerne var blevet klemt åbne og udsat for brøndboringsvæsker.Men undersøgelse af affaldet viste sig at være polymerer med lignende kemi som det kemikalie, der blev brugt som kedelstensinhibitor.Dette fangede vores interesse, og Statoil ønskede at undersøge årsagerne bag disse polymeraffald, der findes i kapillærlinjen.
Kemisk kvalifikation
I et HP HT-felt er der mange udfordringer med hensyn til udvælgelsen af egnede kemikalier til at afbøde de forskellige produktionsproblemer.I kvalificeringen af kedelstensinhibitoren til kontinuerlig injektion nede i hullet blev følgende test udført:
● Produktstabilitet
● Termisk ældning
● Dynamiske præstationstests
● Forenelighed med formationsvand og hydratinhibitor (MEG)
● Statisk og dynamisk gun king test
● Re-opløsning information vand, frisk kemikalie og MEG
Kemikaliet vil blive injiceret med en forudbestemt doseringshastighed,men vandproduktionen vil ikke nødvendigvis være konstant,altså vandslugning.Ind imellem vandsneglene,når kemikaliet kommer ind i brøndboringen,det vil blive mødt af en varm,hurtigstrømmende strøm af kulbrintegas.Dette svarer til at injicere en kedelstenshæmmer i en gasløft-applikation (Fleming et al. 2003). Sammen med
den høje gastemperatur,risikoen for opløsningsmiddelstripping er ekstrem høj, og gun king kan forårsage blokering af injektionsventilen.Dette er en risiko selv for kemikalier formuleret med opløsningsmidler med højt kogepunkt/lavt damptryk og andre damptryksdæmpende midler (VPD'er). I tilfælde af en delvis blokering,strømning af formationsvand,MEG og/eller frisk kemikalie skal være i stand til at fjerne eller genopløse det dehydrerede eller udtørrede kemikalie.
I dette tilfælde blev en ny laboratorietestrig designet til at replikere strømningsforhold nær injektionsportene ved et HP/HTg som produktionssystem.Resultaterne fra de dynamiske gun king-tests viser, at der under de foreslåede anvendelsesbetingelser blev registreret et betydeligt opløsningsmiddeltab.Dette kan føre til hurtig gun king og eventuel blokering af flowlines.Arbejdet viste derfor, at der eksisterede en relativt betydelig risiko for kontinuerlig kemikalieinjektion i disse brønde forud for vandproduktion og førte til beslutningen om at justere normale opstartsprocedurer for dette felt, hvilket forsinkede kemikalieinjektion, indtil vandgennembrud blev opdaget.
Kvalifikationen af kedelstensinhibitor til kontinuerlig injektion nede i borehullet havde stor fokus på opløsningsmiddelstripping og gun king af kedelstensinhibitoren ved injektionspunktet og i flowline, men potentialet for gun king i selve injektionsventilen blev ikke evalueret.Indsprøjtningsventilen fejlede sandsynligvis på grund af betydeligt opløsningsmiddeltab og hurtig gun king,Fig.6. Resultaterne viser, at det er vigtigt at have et holistisk syn på systemet;ikke kun fokusere på produktionsudfordringerne,men også udfordringer relateret til injektion af kemikaliet,dvs. indsprøjtningsventil.
Erfaring fra andre områder
En af de tidlige rapporter om problemer med langdistance kemikalieinjektionslinjer var fra Gull fak sandVig dis satellitfelterne (Osa etal.2001). De undersøiske injektionslinjer var blokeret fra hydratdannelse i linjen på grund af invasion af gas fra de producerede væsker ind i ledningen via indsprøjtningsventilen.Nye retningslinjer for udvikling af undersøiske produktionskemikalier blev udviklet.Kravene omfattede partikelfjernelse (filtrering) og tilsætning af hydratinhibitor (f.eks. glykol) til alle vandbaserede kedelstensinhibitorer, der skulle injiceres ved undersøiske skabeloner.Kemisk stabilitet,viskositet og kompatibilitet (væske og materialer) blev også overvejet.Disse krav er blevet taget længere ind i Statoil-systemet og omfatter kemikalieinjektion i borehullet.
Under udviklingsfasen af Oseberg S eller feltet blev det besluttet, at alle brønde skulle afsluttes med DHC I-systemer (Fleming et al. 2006). Målet var at forhindre CaCO;afskalning i den øvre slange ved SI-injektion.En af de store udfordringer med hensyn til de kemiske injektionslinjer var at opnå kommunikation mellem overfladen og borehullets udløb.Den indvendige diameter af den kemiske injektionsledning blev indsnævret fra 7 mm til 0,7 mm (ID) omkring annulus-sikkerhedsventilen på grund af pladsbegrænsninger, og væskens evne til at blive transporteret gennem denne sektion havde påvirket succesraten.Flere platformsbrønde havde kemikalieinjektionsledninger, der var tilstoppet,men årsagen blev ikke forstået.Tog af forskellige væsker (glykol,rå,kondensat,xylen,skælhæmmer,vand osv.) blev laboratorietestet for viskositet og kompatibilitet og pumpet fremad og i omvendt flow for at åbne ledningerne;imidlertid,målskala-hæmmeren kunne ikke pumpes helt ned til kemikalieindsprøjtningsventilen.Yderligere,komplikationer blev set med udfældning af phosphonat-skala-hæmmeren sammen med resterende CaClz-komplettering-saltlage i én brønd og gun king of the scale-inhibitoren inde i en brønd med højt gasolieforhold og lavt vandudslip (Fleming et al. 2006)
Erfaringer
Testmetodeudvikling
De vigtigste erfaringer fra fejlen i DHC I-systemer har været med hensyn til den tekniske effektivitet af kedelstensinhibitoren og ikke med hensyn til funktionaliteten og kemisk injektion.Topside-injektion og subsea-injektion har fungeret godt overarbejde;imidlertid,applikationen er blevet udvidet til at omfatte kemikalieinjektion nede i borehullet uden en tilsvarende opdatering af de kemiske kvalificeringsmetoder.Statoils erfaring fra de to præsenterede feltsager er, at den styrende dokumentation eller retningslinjer for kemikaliekvalificering skal opdateres til at omfatte denne type kemikalieanvendelse.De to vigtigste udfordringer er blevet identificeret som i) vakuum i kemikalieinjektionslinjen og ii) potentiel udfældning af kemikaliet.
Fordampning af kemikaliet kan forekomme på produktionsslangen (som set i gun king-huset) og i injektionsslangen (en transient grænseflade er blevet identificeret i vakuumkassen) er der risiko for, at disse bundfald kan flyttes med strømmen og ind i injektionsventilen og videre ind i brønden.Indsprøjtningsventilen er ofte udformet med et filter opstrøms for indsprøjtningspunktet,dette er en udfordring,som i tilfælde af nedbør kan dette filter være tilstoppet, hvilket får ventilen til at svigte.
Observationerne og de foreløbige konklusioner fra de indhøstede erfaringer resulterede i en omfattende laboratorieundersøgelse af fænomenerne.Det overordnede mål var at udvikle nye kvalificeringsmetoder for at undgå lignende problemer i fremtiden.I denne undersøgelse er der udført forskellige tests, og adskillige laboratoriemetoder er designet (udviklet med henblik på) at undersøge kemikalier med hensyn til de identificerede udfordringer.
● Filterblokeringer og produktstabilitet i lukkede systemer.
● Virkningen af delvist opløsningsmiddeltab på kemikaliernes korrosivitet.
● Effekten af delvist opløsningsmiddeltab i en kapillar på dannelsen af faste stoffer eller viskøse propper.
Under testene af laboratoriemetoderne er der blevet identificeret flere potentielle problemer
● Gentagne filterblokeringer og dårlig stabilitet.
● Dannelse af faste stoffer efter delvis fordampning fra en kapillær
● PH-ændringer på grund af opløsningsmiddeltab.
Arten af de udførte test har også givet yderligere information og viden vedrørende ændringer i kemikaliers fysiske egenskaber i kapillærer, når de er udsat for visse betingelser,og hvordan dette adskiller sig fra bulk-opløsninger under lignende forhold.Testarbejdet har også identificeret betydelige forskelle mellem bulkvæsken,dampfaser og resterende væsker, som kan føre til enten øget potentiale for nedbør og/eller øget korrosivitet.
Testproceduren for ætsning af kalkinhibitorerne blev udviklet og inkluderet i den styrende dokumentation.For hver applikation skulle der udføres udvidet korrosivitetstest, før injektion af kalkinhibitor kan implementeres.Gun king-tests af kemikaliet i injektionslinjen er også blevet udført.
Forud for påbegyndelse af kvalificering af et kemikalie er det vigtigt at skabe et arbejdsomfang, der beskriver kemikaliets udfordringer og formål.I den indledende fase er det vigtigt at identificere hovedudfordringerne for at kunne udvælge de typer kemikalier, der skal løse problemet.En oversigt over de vigtigste acceptkriterier kan findes i tabel 2.
Kvalificering af kemikalier
Kvalificering af kemikalier består af både test og teoretiske vurderinger for hver ansøgning.Tekniske specifikationer og testkriterier skal defineres og etableres,for eksempel indenfor HSE,materialekompatibilitet,produktstabilitet og produktkvalitet (partikler).Yderligere,frysepunktet,viskositet og kompatibilitet med andre kemikalier,hydrathæmmer,dannelsesvand og den producerede væske skal bestemmes.En forenklet liste over testmetoder, der kan bruges til kvalificering af kemikalier, er angivet i tabel 2.
Løbende fokus på og overvågning af den tekniske effektivitet,doseringssatser og HSE-fakta er vigtige.Kravene til et produkt kan ændre en marks eller et procesanlægs levetid;variere med produktionshastigheder samt væskesammensætning.Opfølgningsaktivitet med evaluering af præstation,optimering og/eller test af nye kemikalier skal udføres hyppigt for at sikre det optimale behandlingsprogram.
Afhængig af oliekvaliteten,vandproduktion og tekniske udfordringer på offshore produktionsanlægget,brugen af produktionskemikalier kan være nødvendig for at opnå eksportkvalitet,myndighedskrav,og at drive offshoreanlægget på en sikker måde.Alle felter har forskellige udfordringer, og de nødvendige produktionskemikalier vil variere fra felt til felt og overarbejde.
Det er vigtigt at fokusere på teknisk effektivitet af produktionskemikalier i et kvalifikationsprogram,men det er også meget vigtigt at fokusere på kemikaliets egenskaber,såsom stabilitet,produktkvalitet og kompatibilitet.Kompatibilitet i denne indstilling betyder kompatibilitet med væskerne,materialer og andre produktionskemikalier.Dette kan være en udfordring.Det er ikke ønskeligt at bruge et kemikalie til at løse et problem for senere at opdage, at kemikaliet bidrager til eller skaber nye udfordringer.Det er måske kemikaliets egenskaber og ikke den tekniske udfordring, der er den største udfordring.
Særlige krav
Særlige krav til filtrering af leverede produkter bør stilles til undersøiske system og for kontinuerlig indsprøjtning nede i hullet.Sil og filtre i det kemiske injektionssystem skal leveres baseret på specifikationen på nedstrømsudstyret fra topside-injektionssystemet,pumper og indsprøjtningsventiler,til indsprøjtningsventilerne i borehullet.Hvor kontinuerlig injektion af kemikalier nede i borehullet anvendes, bør specifikationen i kemikalieinjektionssystemet baseres på specifikationen med den højeste kritikalitet.Dette er måske filteret ved indsprøjtningsventilen nede i hullet.
Indsprøjtningsudfordringer
Injektionssystemet kan indebære 3-50 km afstand af umbilical undersøisk flowline og 1-3 km ned i brønden.Fysiske egenskaber som viskositet og evnen til at pumpe kemikalierne er vigtige.Hvis viskositeten ved havbundstemperaturen er for høj, kan det være en udfordring at pumpe kemikaliet gennem kemikalieinjektionsledningen i undersøisk umbilical og til undersøisk injektionspunkt eller i brønden.Viskositeten skal være i overensstemmelse med systemspecifikationen ved forventet opbevarings- eller driftstemperatur.Dette bør vurderes i hvert enkelt tilfælde,og vil være systemafhængig.Som tabel er kemisk injektionshastighed en faktor for succes i kemisk injektion.For at minimere risikoen for tilstopning af kemikalieinjektionsledningen,kemikalierne i dette system bør være hydrathæmmet (hvis der er potentiale for hydrater).Forenelighed med væsker til stede i systemet (konserveringsvæske) og hydratinhibitoren skal udføres.Stabilitetstest af kemikaliet ved faktiske temperaturer (lavest mulig omgivelsestemperatur,omgivelsestemperatur,undersøisk temperatur,injektionstemperatur) skal passeres.
Der skal også overvejes et program til vask af kemikalieinjektionsslangerne ved en given frekvens.Det kan have en forebyggende effekt at skylle kemikalieinjektionsslangen regelmæssigt med opløsningsmiddel,glykol eller rengøringskemikalier for at fjerne mulige aflejringer, før det akkumuleres og kan forårsage tilstopning af ledningen.Den valgte kemiske opløsning af skyllevæske skal værekompatibel med kemikaliet i injektionslinjen.
I nogle tilfælde bruges kemikalieinjektionslinjen til flere kemiske anvendelser baseret på forskellige udfordringer over en feltlevetid og væskeforhold.I den indledende produktionsfase før vandgennembrud kan hovedudfordringerne være anderledes end dem i den sene levetid, ofte relateret til øget vandproduktion.At skifte fra en ikke-vandig opløsningsmiddelbaseret inhibitor såsom asfaltene-hæmmer til vandbaseret kemikalie såsom kedelstensinhibitor kan give udfordringer med kompatibilitet.Det er derfor vigtigt at fokusere på kompatibilitet og kvalifikation og anvendelse af afstandsstykker, når det er planlagt at skifte kemikalie i kemikalieinjektionslinjen.
Materialer
Med hensyn til materialekompatibilitet,alle kemikalier skal være kompatible med tætninger,elastomerer,pakninger og byggematerialer, der anvendes i det kemiske injektionssystem og produktionsanlægget.Testprocedure for ætsning af kemikalier (f.eks. sur kedelstensinhibitor) til kontinuerlig injektion nede i hullet bør udvikles.For hver applikation skal der udføres udvidet korrosivitetstest, før injektion af kemikalier kan implementeres.
Diskussion
Fordelene og ulemperne ved kontinuerlig kemisk injektion nede i borehullet skal vurderes.Kontinuerlig injektion af kedelstensinhibitor for at beskytte DHS Vor produktionsslangen er en elegant metode til at beskytte brønden mod belægninger.Som nævnt i dette papir er der adskillige udfordringer med kontinuerlig kemisk injektion nede i borehullet,men for at reducere risikoen er det vigtigt at forstå de fænomener, der er forbundet med løsningen.
En måde at reducere risikoen på er at fokusere på udvikling af testmetoder.Sammenlignet med topside- eller undersøisk kemikalieinjektion er der andre og mere alvorlige forhold nede i brønden.Kvalificeringsproceduren for kemikalier til kontinuerlig injektion af kemikalier nede i borehullet skal tage hensyn til disse ændringer i forhold.Kvalificeringen af kemikalierne skal ske efter det materiale, kemikalierne kan komme i kontakt med.Kravene til kompatibilitetskvalificering og test under forhold, der replikerer så tæt som muligt de forskellige brøndlivscyklusforhold, som disse systemer vil arbejde under, skal opdateres og implementeres.Testmetodeudviklingen skal videreudvikles til mere realistiske og repræsentative tests.
Ud over,samspillet mellem kemikalierne og udstyret er afgørende for succes.Udviklingen af de kemiske injektionsventiler skal tage hensyn til de kemiske egenskaber og placeringen af injektionsventilen i brønden.Det bør overvejes at inkludere reelle indsprøjtningsventiler som en del af testudstyret og at udføre præstationstest af kalkinhibitoren og ventildesignet som en del af kvalifikationsprogrammet.At kvalificere skalahæmmere,hovedfokus har tidligere været på procesudfordringerne og skalahæmning,men god skalahæmning afhænger af stabil og kontinuerlig injektion.Uden stabil og kontinuerlig injektion vil potentialet for belægninger øges.Hvis kalkinhibitorindsprøjtningsventilen er sprøjtet, og der ikke er nogen kalkinhibitorinjektion i væskestrømmen,brønden og sikkerhedsventilerne er ikke beskyttet mod belægninger, og derfor kan sikker produktion bringes i fare.Kvalificeringsproceduren skal tage sig af udfordringerne i forbindelse med injektionen af kedelstenshæmmeren ud over procesudfordringerne og effektiviteten af den kvalificerede kedelstenshæmmer.
Den nye tilgang involverer flere discipliner, og samarbejdet mellem disciplinerne og de respektive ansvarsområder skal afklares.I denne applikation topside processystemet,undersøiske skabeloner og brønddesign og færdiggørelser er involveret.Multidisciplinære netværk med fokus på at udvikle robuste løsninger til kemiske injektionssystemer er vigtige og måske vejen til succes.Kommunikation mellem de forskellige discipliner er afgørende;især tæt kommunikation mellem de kemikere, der har kontrol over de anvendte kemikalier, og brøndingeniørerne, der har styr på det udstyr, der bruges i brønden.At forstå de forskellige discipliners udfordringer og at lære af hinanden er essentielt for at forstå kompleksiteten i hele processen.
Konklusion
● Kontinuerlig injektion af kedelstensinhibitor for at beskytte DHS Vor produktionsslangen er en elegant metode til at beskytte brønden for kedelsten
● At løse de identificerede udfordringer,følgende anbefalinger er:
● Der skal udføres en dedikeret DHCI-kvalifikationsprocedure.
● Kvalifikationsmetode for kemikalieindsprøjtningsventiler
● Test- og kvalificeringsmetoder for kemisk funktionalitet
● Metodeudvikling
● Relevant materialetest
● Det tværfaglige samspil, hvor kommunikation mellem de forskellige involverede discipliner er afgørende for succes.
Anerkendelser
Forfatteren ønsker at takke Statoil AS A for tilladelsen til at udgive dette værk og Baker Hughes og Schlumberger for at tillade brug af billedet i Fig.2.
Nomenklatur
(Ba/Sr)SO4=barium/strontiumsulfat
CaCO3=calciumcarbonat
DHCI=kemikalieindsprøjtning nede i borehullet
DHSV = sikkerhedsventil nede i hullet
fx=f.eks
GOR=gasolieforhold
HSE=sundhedssikkerhedsmiljø
HPHT=højtryk høj temperatur
ID=indvendig diameter
dvs.=det vil sige
km=kilometer
mm = millimeter
MEG = monoethylenglycol
mMD=meter målt dybde
OD = udvendig diameter
SI=skalainhibitor
mTV D=meter total lodret dybde
U-rør=U-formet rør
VPD = damptryksdæmpende middel
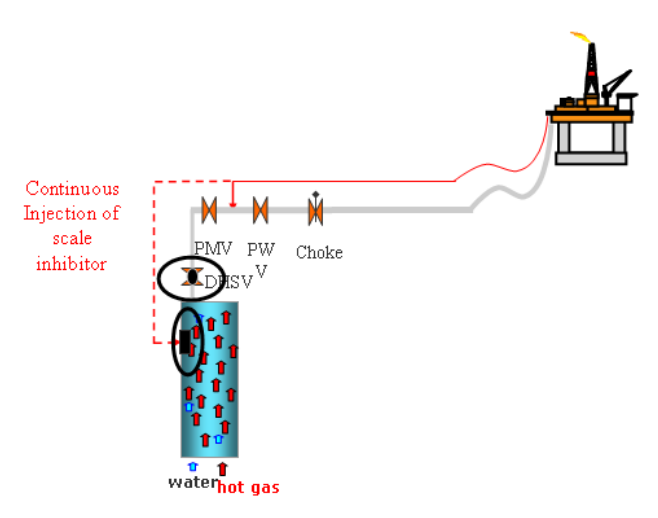
Figur 1. Oversigt over de undersøiske og nede i hullets kemiske injektionssystemer i atypisk område.Skitse af kemikalieinjektion opstrøms DHSV og de relaterede forventede udfordringer.DHS V=downhole sikkerhedsventil, PWV=proces wing ventil og PM V=proces master ventil.
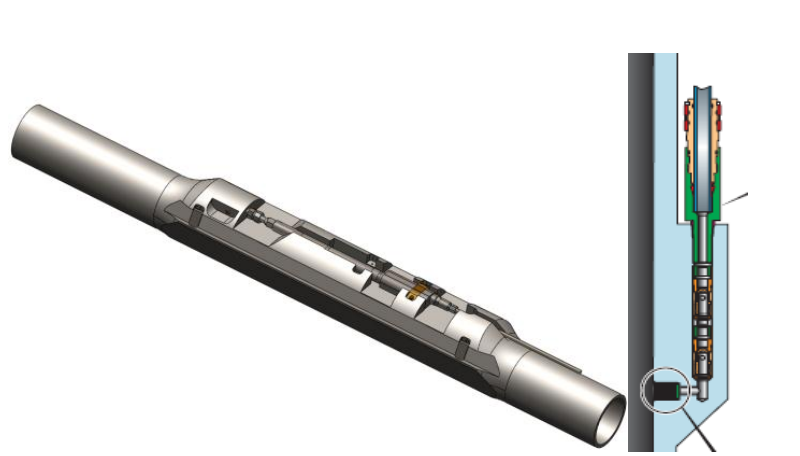
Figur 2. Skitse af atypisk kemisk injektionssystem i borehullet med dorn og ventil.Systemet tilsluttes til overflademanifolden, føres igennem og forbindes til slangeophænget på den ringformede side af slangen.Den kemiske injektionsdorn placeres traditionelt dybt i brønden med den hensigt at give kemisk beskyttelse.
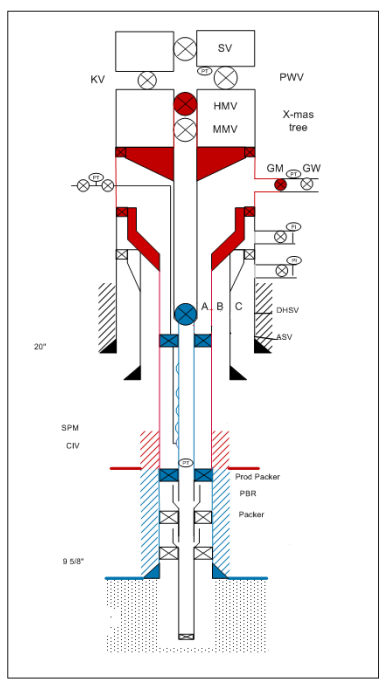
Figur 3. Typisk brøndbarriereskema,hvor den blå farve repræsenterer den primære brøndbarrierekappe;i dette tilfælde produktionsrøret.Den røde farve repræsenterer den sekundære barrierekonvolut;huset.På venstre side er angivet den kemiske injektion, sort linje med injektionspunkt til produktionsslangen i området markeret rødt (sekundær barriere).
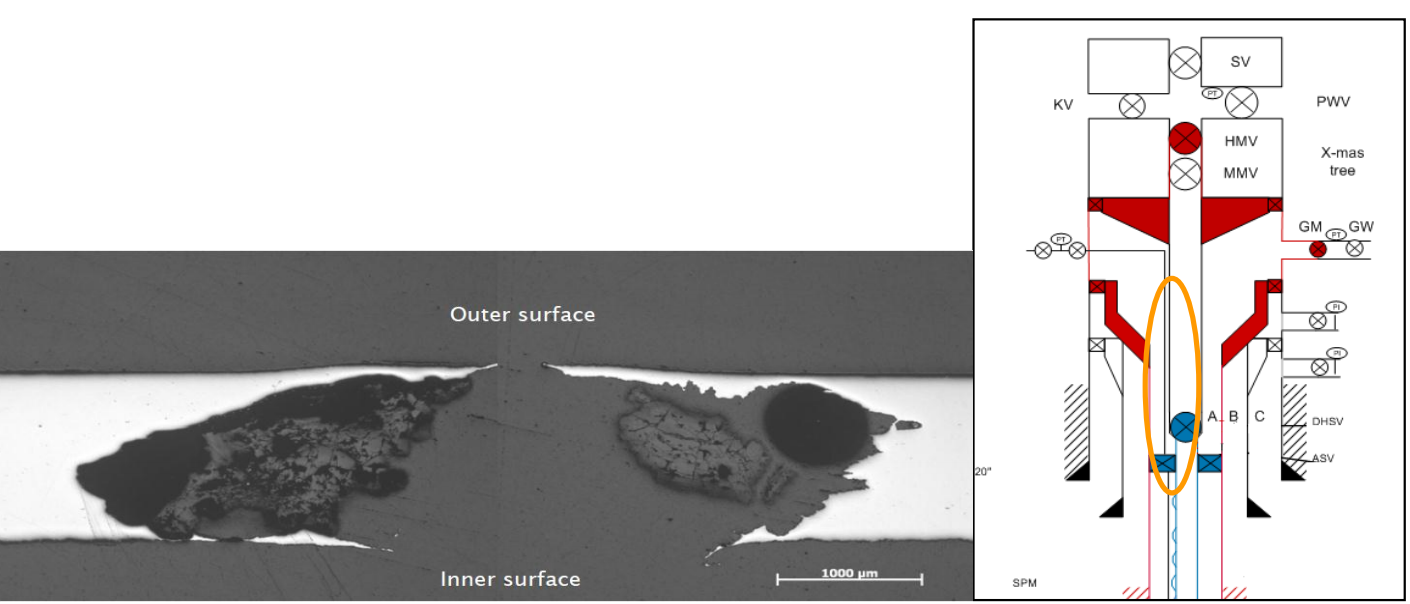
Figur 4. Udhulet hul fundet i den øverste sektion af 3/8” injektionslinjen.Området er vist på skitsen af atypisk brøndbarriere skematisk, markeret med orange ellipse.
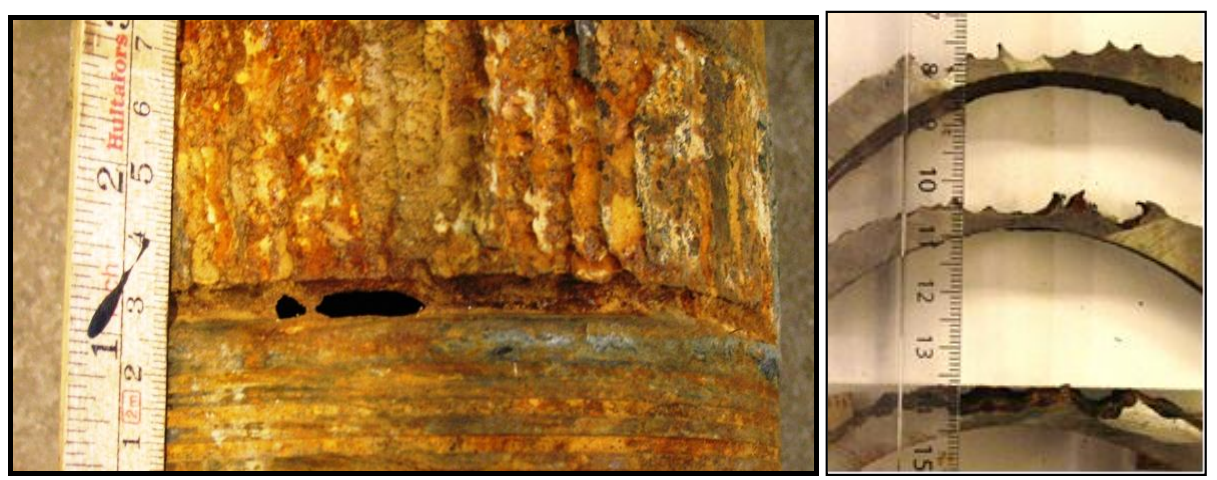
Figur 5. Alvorligt korrosionsangreb på 7” 3 % kromrør.Figuren viser korrosionsangrebet efter kedelstensinhibitor sprøjtet fra den udhulede kemiske injektionslinje på produktionsrøret.
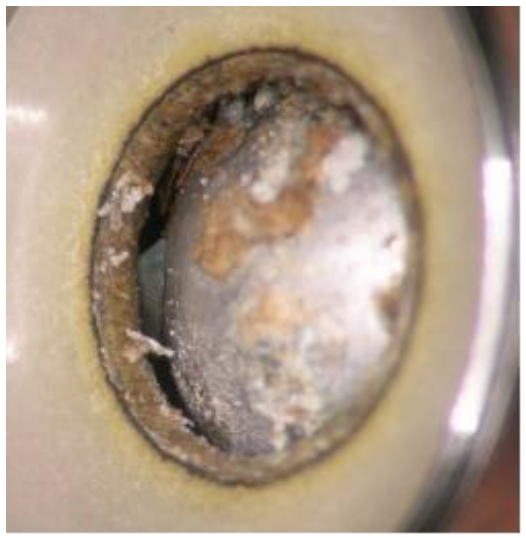
Figur 6. Affald fundet i kemikalieindsprøjtningsventilen.Affaldet i dette tilfælde var metalspåner sandsynligvis fra installationsprocessen foruden noget hvidligt affald.Undersøgelse af det hvide affald viste sig at være polymerer med lignende kemi som det injicerede kemikalie
Indlægstid: 27. april 2022